Blast furnaces
Blast furnace group
Period of construction: 1883 to 1916,
after which the blast furnaces were relined with fireclay bricks every 10-15 years.
In operation: 103 years until the works were decommissioned
The downcomers, which give shape to the silhouette of the works, guided the gas out of the six blast furnaces. The blast furnaces themselves – the first one was built in 1883 – are almost impossible to detect, hidden behind scaffolding, pipes, the wind heaters and chimneys. An average of 130 tons of pig iron were tapped here at intervals of 2½ to 3 hours, around 1,100 tons per blast furnace. The wind heaters are positioned in front of the blast furnaces in groups of three. They heated the blast furnace wind of the blower machines to 1,200°C. Temperatures in the bottom area of the blast furnace reached up to 2,200°C.
The inclined ore lift
All six blast furnaces were filled with raw materials via a single track system. The electric monorail system was built between 1911 and 1918. The track is almost 6 kilometres long in total. An average of 310 monorail cars travelled along it to supply the blast furnaces, and their squeaking could be heard day and night all over Völklingen.
However, this construction meant that the blast furnaces could not be enlarged. The sloping lift had been designed for a height of precisely 27 metres. Production at the Völklingen Ironworks could no longer keep pace with the development of the iron-producing industry.
A similar sloping ore lift on the back of the blast furnace group brought the coke produced in the coking plant to charge level on the charging platform.
Cowper
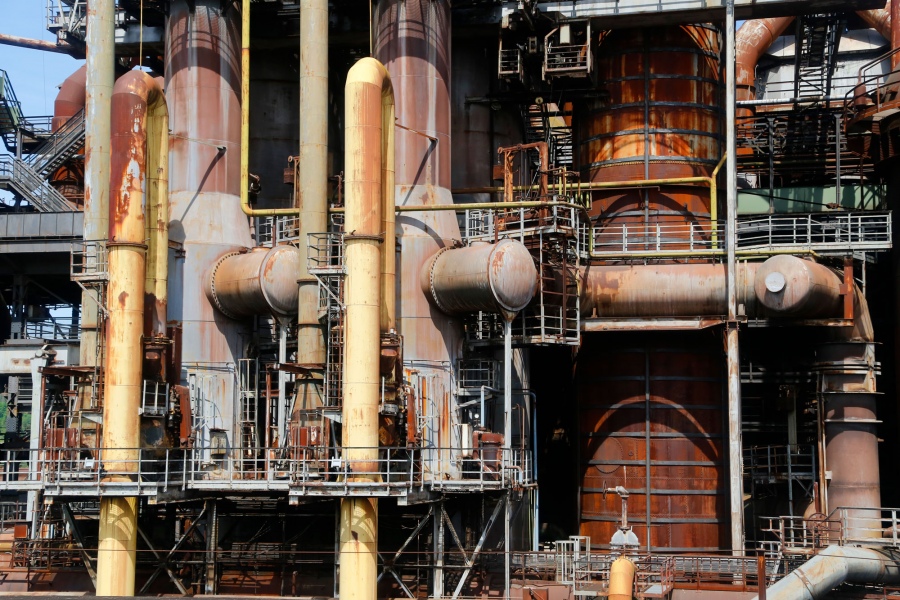
Detail of the cowper of blast furnace six
Copyright: Weltkulturerbe Völklinger Hütte | Karl Heinrich Veith
The blast heating apparatus (Cowper) of the Völklingen Ironworks is up to 40 metres
tall. Like the blast furnaces themselves, it is among the largest constructions
in the blast furnace group with its diameter of up to 7 metres. The brickwork
on the inside of the blast heating apparatus was heated up by the gas. After
this, the heating was turned off and the cold blast from the blowers passed
through the blast heating apparatus. By this means, the blast was heated to
a temperature of up to 1200°C before being blown into the furnace. On blast
heating apparatus 6.3 - the no. 3 heater of no. 6 furnace - the inscription
'Cold blast' can clearly be made out on the pipe.
Charging Platform
The charging platform connects all six blast furnaces on one level. The monorail cars are guided along this level. The charging platform is about 240 metres long and exactly 27 metres high. Its name has its root in the verb "to charge", which here means filling the blast furnaces with the raw materials for iron production. Iron ore, sinter, additives, coke and ferrous residues from industry or scrap materials were tipped into the charging hopper of the blast furnace. The "hood", the upper closure of the blast furnace, was raised, then five monorail cars were driven around the funnel. There was a second closure below the hood, the "bell". It remained closed in order to collect the furnace gas. The material was tipped onto the bell and the hood then lowered. The bell was only moved down once the hood was closed. The material slid down into the blast furnace shaft.
Blast fournaces
Blast Furnaces
The six blast furnaces of the Völklingen ironworks are all 27 metres high with an outer diameter of almost 10 metres. They were built between 1888 and 1916, but were renewed, rebuilt and extended several times after that.
The blast furnaces as they are today date back to the 1970s, had a capacity of more than 1,000 m3, and are surrounded by a 3 cm thick sheet steel sleeve. They are lined with fireproof bricks on the inside. The lining is 60 cm thick in the upper part of the blast furnaces and 1 metre in the lower part, where the heat is greater.
However, even this mighty masonry was not enough to tame the scorching heat inside the blast furnace. Water constantly trickled down the outer walls as well to cool the sleeve.
The blast furnace tapping
well to cool the sleeve.
The blast-furnace-man tapped the blast furnace every 2 to 2½ hours. There were two tapping holes for pig iron and slag in the steel sleeve. These holes were filled with a clay slate mass that the blast-furnace-man could drill open and seal off again. In the past, the blast-furnace-man would have used a pneumatic hand drill and oxygen lance to open the tapping hole; later this was done using a remote-controlled drill. 130 tons of liquid pig iron flowed through the tapping channel into the torpedo car that brought the iron to the steelworks. The pig iron flowed out of the tapping hole at a temperature of over 1,400°C. Extrapolated, this resulted in a daily output of approx. 6,000 tons of pig iron for all six blast furnaces. Today's blast furnaces can produce more than 10,000 tons of pig iron in 24 hours, far more than all six of the Völklingen blast furnaces combined.